In the hustle of industrial spaces, construction zones, and even office environments, noise and lighting often take a backseat in safety discussions. However, both play a critical role in not only productivity but also the health and safety of workers. Adhering to prescribed noise and illumination standards isn’t just about compliance — it’s about creating a workplace where people thrive, think clearly, and stay safe.
Understanding the Impact of Noise in Workplaces
Excessive noise is more than just an annoyance. Prolonged exposure can lead to permanent hearing loss, increased stress levels, communication barriers, and reduced concentration. This can result in mistakes, poor decision-making, and in high-risk industries, even fatal accidents.
According to the Occupational Safety and Health Administration (OSHA), noise levels exceeding 85 decibels (dB) over an 8-hour shift require hearing protection and control measures. In India, OSPCB and other regulatory bodies align with similar benchmarks for industrial noise standards.
Common sources of workplace noise include:
- Machinery and equipment
- Generators and compressors
- Power tools
- Vehicle and transport operations
Solutions to manage noise levels:
- Acoustic enclosures and barriers
- Use of silencers or mufflers on machinery
- Personal Protective Equipment (PPE) like earplugs and earmuffs
- Regular noise audits and monitoring
The Role of Proper Illumination
Proper lighting is just as essential. Insufficient or harsh lighting can lead to eye strain, increased accident risk, lowered morale, and reduced accuracy in tasks. Every workspace, from manufacturing units to laboratories and offices, requires task-specific illumination.
BIS standards (IS 3646) outline minimum lux levels for various work environments. For instance:
- General assembly tasks: 300–500 lux
- Precision workstations: 750–1000 lux
- Corridors and general spaces: 100–200 lux
Key Illumination Best Practices:
- Use of glare-free, energy-efficient lighting
- Regular maintenance and cleaning of lighting fixtures
- Smart lighting systems for automatic adjustment
- Task-specific lighting at workbenches or inspection areas
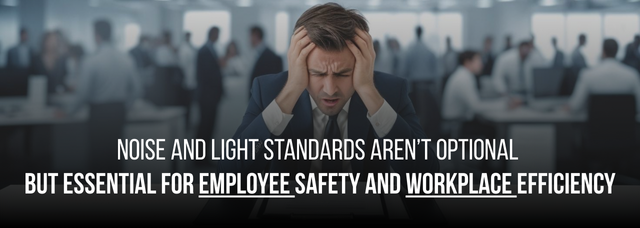
Why Compliance is Not Optional ?
Ignoring noise and illumination standards can result in regulatory penalties, reduced workforce efficiency, and long-term health consequences for employees. More importantly, non-compliance compromises workplace safety — which should always be a top priority.
Creating a Culture of Safety
Organizations that invest in workplace environmental monitoring demonstrate responsibility toward their people. Conducting regular noise and illumination audits, offering training, and integrating modern monitoring technologies ensures not only compliance but also a safe, comfortable, and productive work culture.
Conclusion
Creating a safe and productive workplace isn’t just about meeting legal obligations—it’s about valuing your people and their well-being. Noise and illumination standards are not just technical requirements; they are essential components of a work environment that supports focus, reduces health risks, and prevents accidents. By regularly assessing and upgrading these conditions, businesses can foster a culture of safety, enhance employee satisfaction, and improve overall operational efficiency. Investing in the right standards today leads to a healthier, more sustainable workplace tomorrow.